Control Estadístico de Procesos: Aprende cómo mejorar tu producción con datos precisos
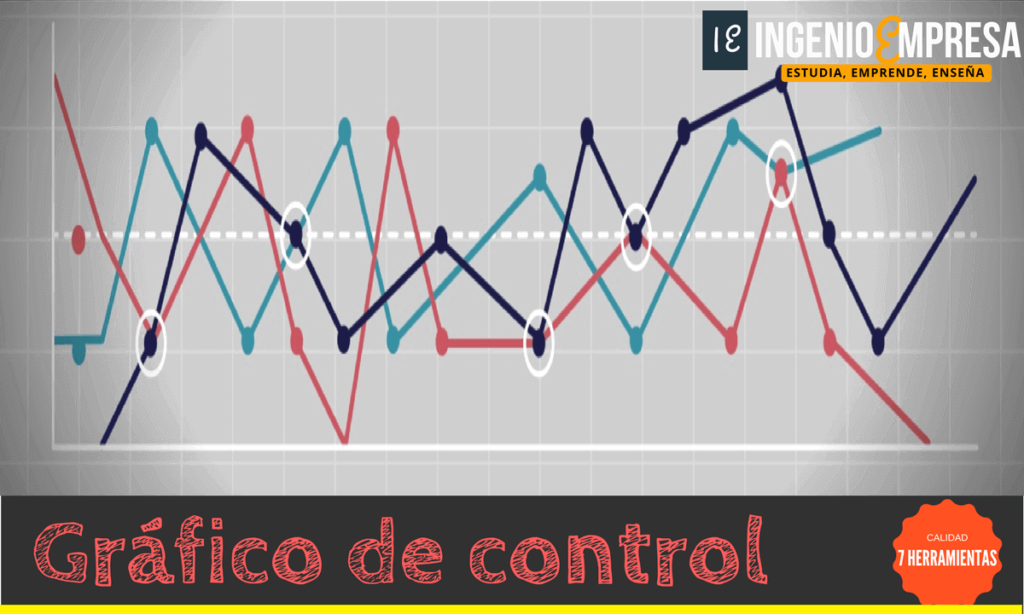
El control estadístico de procesos es una herramienta esencial para cualquier empresa que desee mejorar la calidad de sus productos o servicios. Mediante el análisis de datos y la aplicación de técnicas estadísticas, permite identificar y corregir los problemas en el proceso de producción, evitando defectos y pérdidas innecesarias.
Exploraremos en detalle qué es el control estadístico de procesos, cómo se lleva a cabo y cuáles son las principales técnicas utilizadas. Además, analizaremos los beneficios de implementar esta metodología en una organización y cómo puede contribuir a optimizar la producción y alcanzar los estándares de calidad deseados. Si estás interesado en mejorar la eficiencia y competitividad de tu empresa, no te pierdas este completo análisis sobre el control estadístico de procesos.
- Qué es el control estadístico de procesos y cómo puede mejorar la producción
- Cuáles son los beneficios de utilizar el control estadístico de procesos en una empresa
- Cuáles son los datos necesarios para implementar el control estadístico de procesos
- Cómo se recopilan y analizan los datos en el control estadístico de procesos
- Cuáles son las herramientas más comunes utilizadas en el control estadístico de procesos
- Cómo interpretar y utilizar los gráficos de control en el control estadístico de procesos
- Cuáles son las principales causas de variación en un proceso y cómo se pueden identificar mediante el control estadístico
- Cómo se establecen los límites de control en el control estadístico de procesos
- Qué medidas correctivas se pueden tomar cuando se detecta una variación fuera de los límites de control
- Cuáles son algunas estrategias para mantener un control estadístico de procesos efectivo a largo plazo
- Cuáles son algunos ejemplos reales de implementación exitosa del control estadístico de procesos en diferentes industrias
- Preguntas frecuentes (FAQ)
Qué es el control estadístico de procesos y cómo puede mejorar la producción
El control estadístico de procesos (CEP) es una metodología utilizada en la gestión de la calidad para monitorear y mejorar los procesos productivos. Se basa en analizar y controlar los datos recopilados durante la producción con el objetivo de detectar desviaciones, reducir la variabilidad y optimizar la eficiencia del proceso.
El CEP utiliza herramientas estadísticas para analizar los datos y tomar decisiones informadas sobre cómo mejorar el proceso. A través de la recopilación sistemática de información, se pueden identificar las causas de las variaciones y se pueden implementar acciones correctivas para garantizar que el proceso opere dentro de los límites establecidos.
Beneficios del control estadístico de procesos
- Mejora de la calidad: El CEP permite identificar problemas o desviaciones en el proceso de producción de manera temprana, lo que ayuda a evitar defectos y mejorar la calidad del producto final.
- Reducción de costos: Al optimizar el proceso y reducir la variabilidad, se pueden reducir los costos asociados con reprocesos, desperdicios y retrabajos.
- Aumento de la eficiencia: Mediante el control y la optimización continua del proceso, se puede aumentar la eficiencia operativa, lo que resulta en una mayor productividad y rentabilidad.
- Mayor satisfacción del cliente: Al asegurar una mayor consistencia en la calidad del producto o servicio, se logra una mayor satisfacción por parte de los clientes.
El CEP se puede aplicar en diferentes industrias y sectores, desde la fabricación hasta los servicios. Permite tener un mayor control sobre los procesos y una toma de decisiones basada en datos, lo que resulta en una mejora continua y sostenible de la producción.
Cómo implementar el control estadístico de procesos
- Definir el objetivo: Es importante establecer claramente qué se desea lograr con el control estadístico de procesos. Puede ser mejorar la calidad, reducir costos, aumentar la eficiencia, entre otros.
- Recopilar datos: Se deben recopilar datos relevantes sobre el proceso que se quiere controlar. Esto puede incluir mediciones de variables clave, tiempos de producción, muestras de productos, etc.
- Analizar los datos: Utilizando herramientas estadísticas, como gráficos de control, histogramas y análisis de capacidad, se deben analizar los datos para determinar la variabilidad y las tendencias del proceso.
- Establecer límites de control: Los límites de control son valores establecidos que indican la variabilidad esperada en el proceso. Si los datos se encuentran dentro de estos límites, se considera que el proceso está bajo control.
- Tomar acciones correctivas: Si se detectan desviaciones significativas o tendencias preocupantes, se deben tomar acciones correctivas para eliminar las causas subyacentes y asegurar que el proceso vuelva a estar bajo control.
- Mantener el monitoreo: El control estadístico de procesos es un proceso continuo. Se deben mantener los registros, actualizar los límites de control si es necesario y seguir monitoreando para garantizar que el proceso se mantenga bajo control.
El control estadístico de procesos es una herramienta poderosa para mejorar la producción y garantizar la calidad de los productos o servicios. Al analizar y controlar los datos con precisión, se pueden identificar problemas, reducir la variabilidad y optimizar la eficiencia del proceso, lo que resulta en una mejora continua y sostenible de la producción.
Cuáles son los beneficios de utilizar el control estadístico de procesos en una empresa
El control estadístico de procesos (CEP) es una herramienta poderosa que puede ayudar a las empresas a mejorar su producción y optimizar sus operaciones. Al implementar el CEP, las organizaciones pueden monitorear y controlar sistemáticamente los procesos clave, con el objetivo final de garantizar la calidad del producto o servicio entregado.
Uno de los principales beneficios de utilizar el control estadístico de procesos es la capacidad de detectar desviaciones o variaciones en el proceso productivo. Mediante el análisis de datos recopilados en tiempo real, el CEP permite identificar problemas antes de que se conviertan en defectos o fallas mayores, lo que ahorra tiempo y recursos valiosos para la empresa.
Otro beneficio importante del CEP es su capacidad para brindar una visión clara y objetiva de cómo está funcionando un determinado proceso. Al analizar los datos recopilados, se pueden identificar patrones y tendencias que indican si el proceso está bajo control o si requiere alguna mejora o ajuste.
Mejor toma de decisiones basada en datos
El control estadístico de procesos también proporciona a las empresas una base sólida para la toma de decisiones fundamentadas en datos precisos y confiables. Al contar con información precisa sobre el rendimiento del proceso, los gerentes y responsables de la toma de decisiones pueden identificar áreas problemáticas y establecer acciones correctivas de manera oportuna.
Además, el CEP permite establecer metas y objetivos claros basados en datos reales. Al medir y analizar continuamente el desempeño del proceso, es posible establecer estándares y metas realistas para mejorar la calidad, reducir los costos, aumentar la eficiencia y lograr una mayor satisfacción del cliente.
- Reducción de variabilidad: El control estadístico de procesos permite identificar fuentes de variabilidad y tomar medidas para reducirla, lo que a su vez mejora la consistencia y estabilidad del proceso.
- Optimización de recursos: Al analizar y comprender mejor el proceso, las empresas pueden optimizar el uso de recursos como materiales, mano de obra y maquinaria, maximizando así la eficiencia y minimizando los costos.
- Mejora continua: Con un enfoque basado en datos y análisis, el CEP promueve la cultura de mejora continua en una empresa. Los hallazgos y lecciones aprendidas durante el seguimiento del proceso pueden utilizarse para implementar mejoras continuas y alcanzar niveles más altos de excelencia operativa.
Utilizar el control estadístico de procesos puede generar múltiples beneficios para una empresa, incluyendo la detección temprana de problemas, una toma de decisiones más informada y fundamentada, la reducción de la variabilidad, la optimización de recursos y la promoción de la mejora continua. Implementar y aprovechar esta herramienta puede marcar la diferencia en la calidad y competitividad de una organización en un mercado exigente.
Cuáles son los datos necesarios para implementar el control estadístico de procesos
Cuando se trata de implementar el control estadístico de procesos, es crucial contar con datos precisos y confiables. Estos datos juegan un papel fundamental en el análisis y la mejora continua de los procesos de producción. En esta sección, exploraremos cuáles son los datos necesarios para llevar a cabo el control estadístico de procesos de manera efectiva.
1. Datos de calidad
El primer paso para implementar el control estadístico de procesos es asegurarse de contar con datos de calidad. Esto significa que los datos deben ser precisos, actualizados y completos. Además, es importante que los datos sean representativos de la población objetivo y que se hayan recopilado de manera constante a lo largo del tiempo.
Para garantizar la calidad de los datos, es recomendable establecer procedimientos claros de recolección y almacenamiento de la información. Asimismo, es necesario capacitar al personal encargado de recopilar los datos, para garantizar que se sigan los protocolos establecidos y se eviten errores o inconsistencias en la recopilación de la información.
2. Datos históricos
Además de los datos de calidad, también es importante contar con datos históricos. Estos datos permiten identificar tendencias y patrones a lo largo del tiempo, lo cual es esencial para realizar un análisis adecuado y tomar decisiones informadas.
Los datos históricos pueden incluir información sobre la variabilidad de los procesos, su desempeño pasado, e incluso datos de eventos o incidencias relevantes que hayan tenido lugar en el pasado. Esta información es valiosa para comprender la evolución de los procesos y detectar posibles problemas o áreas de mejora.
3. Datos de control
Una vez que se cuenta con datos de calidad y datos históricos, es necesario identificar qué datos son relevantes para el control estadístico de procesos. Estos datos se conocen como datos de control y suelen incluir mediciones y registros de variables clave que afectan el desempeño del proceso.
Los datos de control pueden variar según el tipo de proceso y la industria en la que se encuentra. Por ejemplo, en un proceso de manufactura, los datos de control pueden incluir mediciones de tiempo de ciclo, defectos por unidad producida, temperatura, entre otros. En cambio, en un proceso de servicio, los datos de control pueden estar relacionados con el tiempo de atención al cliente, la satisfacción del cliente o la velocidad de respuesta.
4. Datos de referencia
Por último, es común utilizar datos de referencia para el control estadístico de procesos. Estos datos actúan como estándar o punto de referencia con el cual se comparan los datos actuales del proceso. Los datos de referencia pueden provenir de diferentes fuentes, como normas industriales, estándares de calidad, o incluso datos de competidores directos.
Utilizar datos de referencia ayuda a establecer metas y objetivos claros para mejorar el desempeño del proceso. Además, permite identificar desviaciones significativas y tomar acciones correctivas oportunas para mantener el proceso bajo control y dentro de los límites establecidos.
Para implementar el control estadístico de procesos de manera efectiva, es necesario contar con datos de calidad, datos históricos, datos de control y datos de referencia. Estos datos proporcionan la base sólida para el análisis, la mejora continua y la toma de decisiones informadas en la producción.
Cómo se recopilan y analizan los datos en el control estadístico de procesos
En el control estadístico de procesos, la recopilación y análisis de datos desempeñan un papel fundamental para mejorar la producción y garantizar la calidad de los productos o servicios. A través del seguimiento sistemático de diferentes variables y parámetros, es posible detectar cualquier desviación o variación no deseada en los procesos, lo que permite tomar medidas preventivas o correctivas de manera oportuna.
La recopilación de datos se lleva a cabo a través de diferentes métodos y técnicas. Uno de los enfoques más comunes es utilizar hojas de registro, donde los operarios o técnicos encargados de la producción registran manualmente las mediciones relevantes en intervalos de tiempo predefinidos. Estas mediciones pueden incluir variables como dimensiones, pesos, tiempos de ciclo, entre otros, dependiendo del tipo de proceso que se esté controlando.
Además de las hojas de registro, también existen sistemas automatizados de recopilación de datos. Estos sistemas utilizan sensores, instrumentos de medición y dispositivos electrónicos para capturar y almacenar los datos de manera precisa y en tiempo real. Esta automatización no solo agiliza el proceso de recopilación, sino que también minimiza los errores humanos y proporciona una mayor confiabilidad de los datos.
Análisis de datos en el control estadístico de procesos
Una vez recopilados los datos, es momento de analizarlos para obtener información valiosa sobre el desempeño y la estabilidad de los procesos. El análisis estadístico es una herramienta clave en esta etapa, ya que permite identificar patrones, tendencias y anomalías en los datos recopilados.
Una de las técnicas más comunes en el análisis de datos del control estadístico de procesos es el uso de gráficos de control. Estos gráficos permiten visualizar la variabilidad de las mediciones a lo largo del tiempo y establecer límites de control que indican si el proceso se encuentra dentro de los parámetros aceptables o si presenta alguna desviación significativa.
Otra técnica utilizada en el análisis de datos es el cálculo de índices y estadísticas clave. Estos índices proporcionan información sobre la capacidad del proceso para cumplir con las especificaciones o tolerancias establecidas. Algunos ejemplos de estos índices son el índice de capacidad del proceso (Cpk), el índice de rendimiento del proceso (Ppk) y el índice de capacidad potencial del proceso (Pp).
Además de los gráficos y los índices, también se pueden utilizar otras técnicas avanzadas de análisis de datos, como el análisis de varianza (ANOVA) y la regresión lineal. Estas técnicas permiten identificar relaciones entre variables y determinar cuáles son las causas principales de las variaciones en los procesos.
La recopilación y análisis de datos en el control estadístico de procesos son fundamentales para mejorar la producción y garantizar la calidad de los productos o servicios. Mediante la utilización de herramientas estadísticas y técnicas de análisis de datos, es posible identificar desviaciones, tendencias y patrones, lo que permite tomar acciones preventivas o correctivas para optimizar los procesos y maximizar la eficiencia y la calidad.
Cuáles son las herramientas más comunes utilizadas en el control estadístico de procesos
El control estadístico de procesos (CEP) es una gran herramienta utilizada en la industria para mejorar la calidad y eficiencia de los procesos de producción. A través del análisis y seguimiento de los datos recolectados durante el proceso, el CEP permite identificar y corregir desviaciones o anomalías que puedan afectar la calidad del producto final.
Herramienta #1: Gráficas de control
Una de las herramientas más comunes utilizadas en el CEP son las gráficas de control. Estas gráficas permiten monitorear el comportamiento del proceso a lo largo del tiempo, comparando los resultados obtenidos con límites establecidos previamente. Las gráficas de control se dividen en dos tipos principales: gráficas para variables y gráficas para atributos.
Las gráficas para variables se utilizan cuando los datos recolectados son de naturaleza continua y pueden ser medidos de forma precisa. Algunos ejemplos de variables son el peso de un producto, la temperatura de un horno o la resistencia de un material. Para estas gráficas se utilizan diferentes tipos como la gráfica -barra y la gráfica R, que permiten analizar la media y la variabilidad del proceso respectivamente.
Por otro lado, las gráficas para atributos se utilizan cuando los datos recolectados son de naturaleza discreta y solo pueden clasificarse en categorías. Ejemplos de atributos incluyen la presencia o ausencia de un defecto en un producto o el número de defectos encontrados en una muestra. Algunas gráficas para atributos comunes son la gráfica p y la gráfica c, que permiten controlar la proporción de defectos y el número de defectos respectivamente.
Herramienta #2: Análisis de capacidad del proceso
Otra herramienta importante en el CEP es el análisis de capacidad del proceso, que permite determinar si un proceso está bajo control estadístico y si cumple con las especificaciones establecidas. Para realizar este análisis se utilizan diferentes índices de capacidad como el Cp, Cpk y Ppk.
El Cp es una medida de la variabilidad del proceso comparada con las especificaciones de diseño, mientras que el Cpk y el Ppk toman en cuenta tanto la variabilidad como el desplazamiento del proceso con respecto a las especificaciones. Estos índices nos ayudan a evaluar si el proceso es capaz de producir productos dentro de los límites aceptables y si existen oportunidades de mejora.
Herramienta #3: Muestreo por atributos
Otra herramienta clave en el CEP es el muestreo por atributos, que se utiliza cuando no es posible o práctico medir todas las unidades de producción y se deben tomar muestras representativas para su inspección. Con el muestreo por atributos se pueden determinar la cantidad de unidades defectuosas en una muestra y estimar la proporción de defectos en toda la población.
Existen diferentes tipos de planes de muestreo por atributos, como el plan de muestreo simple, doble o múltiple, que definen la cantidad de unidades a inspeccionar y los criterios de aceptación o rechazo basados en los resultados obtenidos.
Herramienta #4: Análisis de tendencias
Finalmente, el análisis de tendencias es una herramienta que permite identificar patrones o cambios en el proceso a lo largo del tiempo. Este análisis se realiza mediante la revisión de los datos recolectados en diferentes periodos y la detección de posibles desviaciones o mejoras.
La identificación de tendencias puede ayudar a detectar problemas en el proceso antes de que se conviertan en defectos o fallas más graves, permitiendo tomar medidas correctivas de manera oportuna. Algunas técnicas comunes utilizadas en el análisis de tendencias son el análisis de regresión y el análisis de series de tiempo.
El control estadístico de procesos utiliza diversas herramientas para monitorear y mejorar los procesos de producción. Las gráficas de control, análisis de capacidad del proceso, muestreo por atributos y análisis de tendencias son solo algunas de las herramientas más comunes utilizadas en el CEP. Estas herramientas proporcionan información precisa y objetiva que permite identificar desviaciones, tomar medidas correctivas y optimizar la calidad y eficiencia de la producción.
Cómo interpretar y utilizar los gráficos de control en el control estadístico de procesos
Los gráficos de control son una herramienta esencial en el control estadístico de procesos (CEP) que permite monitorear y analizar los datos obtenidos durante la producción. Estos gráficos nos brindan información valiosa sobre la variabilidad del proceso y nos ayudan a identificar posibles problemas o desviaciones que puedan surgir.
Al interpretar los gráficos de control, es importante comprender los diferentes elementos que los conforman. En primer lugar, tenemos la línea central, que representa el valor promedio de la variable de interés. Luego, tenemos las líneas de control superior e inferior, que se calculan a partir de los datos y nos indican los límites aceptables dentro de los cuales debe mantenerse el proceso.
Elegir un gráfico de control adecuado
Existen diferentes tipos de gráficos de control, y cada uno de ellos es adecuado para monitorear distintos tipos de variables. Algunos de los gráficos más comunes son:
Gráfico de control -Barra y R
: Este gráfico se utiliza cuando se desea controlar la media y la variabilidad del proceso.Gráfico de control -Barra y S
: Similar al gráfico anterior, pero en lugar de utilizar el rango, utiliza la desviación estándar para medir la variabilidad.Gráfico de control P
: Se utiliza para controlar una proporción o porcentaje, como por ejemplo la cantidad de productos defectuosos en una producción.Gráfico de control C
: Es similar al gráfico P, pero se utiliza para variables discontinuas o en conteo.
La elección del gráfico de control adecuado dependerá de la variable que se esté analizando y el objetivo principal del proceso. Es importante seleccionar el gráfico que mejor se adapte a las características del proceso para obtener resultados más precisos y confiables.
Análisis de los gráficos de control
Al observar un gráfico de control, existen varios patrones o señales que pueden indicar problemas en el proceso. Algunas de estas señales incluyen:
Puntos fuera de los límites de control
: Si algún punto cae por encima o por debajo de las líneas de control, esto puede indicar una falta de control en el proceso.Tendencias o patrones sistemáticos
: Si los puntos en el gráfico muestran una tendencia ascendente o descendente, o si se observan patrones repetitivos, esto puede indicar alteraciones en el proceso.Excesiva variabilidad
: Si los puntos están dispersos ampliamente en el gráfico, esto puede indicar una alta variabilidad en el proceso que debe ser investigada.
Una vez identificados estos patrones o señales, es importante realizar un análisis más detallado para determinar la causa raíz del problema. Esto puede requerir la recopilación de datos adicionales, la realización de pruebas o la implementación de acciones correctivas para restablecer el control del proceso.
Los gráficos de control son una herramienta valiosa en el control estadístico de procesos que nos permite monitorear, analizar y mejorar la producción a partir de datos precisos. Al interpretar estos gráficos y detectar posibles problemas o desviaciones, podemos tomar medidas correctivas oportunas para mantener un proceso controlado y garantizar la calidad de nuestros productos o servicios.
Cuáles son las principales causas de variación en un proceso y cómo se pueden identificar mediante el control estadístico
En cualquier proceso de producción, es normal que se presenten variaciones en los resultados obtenidos. Estas variaciones pueden deberse a diferentes factores, como cambios en las condiciones ambientales, desgaste de equipos, errores humanos, entre otros. Identificar y controlar estas variaciones es fundamental para garantizar una producción de calidad y minimizar los desperdicios.
El control estadístico de procesos (CEP) es una herramienta que permite monitorear y analizar estas variaciones. El objetivo principal del CEP es determinar si un proceso está dentro de los límites aceptables de variación o si es necesario realizar ajustes para mejorar su rendimiento.
Las principales causas de variación en un proceso
- Factores ambientales: Los cambios en la temperatura, humedad, presión, entre otros, pueden influir en las características del producto final. Por ejemplo, en la industria alimentaria, una variación en la temperatura durante la cocción de un alimento puede afectar su textura y sabor.
- Desgaste de equipos: Con el uso constante, los equipos tienden a desgastarse, lo que puede ocasionar variaciones en los resultados. Por ejemplo, en una máquina de empaque, un desgaste en las cuchillas puede conducir a un sellado deficiente de los productos.
- Error humano: Los errores cometidos por los operarios también pueden generar variaciones en un proceso. Un mal manejo de los insumos, una falta de capacitación o simplemente distracciones pueden afectar negativamente la calidad del producto.
- Fallos en el suministro de materiales: La falta de suministro adecuado de materiales esenciales para la producción puede ocasionar interrupciones en el proceso y generar variaciones en los productos finales.
Cómo se pueden identificar estas variaciones mediante el control estadístico
El control estadístico de procesos utiliza herramientas como gráficos de control, histogramas y análisis de capacidad para detectar las variaciones y determinar si estas son atribuibles a causas comunes o especiales. Las causas comunes representan las variaciones inherentes al proceso y deben ser estudiadas para establecer límites de control aceptables. Las causas especiales, por otro lado, son variaciones que deben ser investigadas y corregidas, ya que indican problemas específicos en el proceso.
Para implementar el CEP, es necesario recolectar datos de forma sistemática y periódica durante el proceso de producción. Estos datos pueden utilizarse para calcular medidas estadísticas como media, desviación estándar y rango, que proporcionan información importante sobre la variabilidad del proceso.
Una vez recopilados los datos, se construyen gráficos de control, que permiten visualizar las variaciones y establecer límites de control estadísticamente válidos. Si los puntos en el gráfico están dentro de los límites de control, significa que el proceso está en estado de control y no hay causas especiales presentes. En caso contrario, se deben investigar las causas y tomar acciones correctivas.
Cómo se establecen los límites de control en el control estadístico de procesos
En el control estadístico de procesos, uno de los aspectos fundamentales es la determinación de los límites de control. Estos límites son utilizados para identificar cuando un proceso se encuentra bajo control y cuando presenta variaciones inaceptables.
Existen diferentes métodos para establecer los límites de control, pero uno de los más comunes es utilizando la media y la desviación estándar del proceso. Para ello, se recolectan datos del proceso a lo largo del tiempo y se calcula su media y desviación estándar.
Establecimiento de los límites de control utilizando la media y la desviación estándar
El primer paso para establecer los límites de control es calcular la media del proceso. La media representa el valor promedio de las observaciones y nos permite tener una referencia de cómo debería comportarse el proceso en condiciones normales.
Una vez obtenida la media, se calcula la desviación estándar del proceso. La desviación estándar nos indica qué tan dispersas están las observaciones con respecto a la media. Si la desviación estándar es baja, esto significa que las observaciones tienden a estar muy cerca de la media, mientras que si es alta, implica que las observaciones están más dispersas.
Con la media y la desviación estándar calculadas, se pueden establecer los límites de control. Los límites de control se definen generalmente a 3 desviaciones estándar por encima y por debajo de la media. Esto implica que la mayoría de las observaciones deberían caer dentro de estos límites, mientras que aquellas que estén fuera podrían indicar una variación inaceptable del proceso.
Es importante tener en cuenta que el establecimiento de los límites de control utilizando la media y la desviación estándar es solo uno de los métodos disponibles. Otros métodos incluyen el uso de rangos, mediano rango y otras técnicas más avanzadas basadas en modelos estadísticos.
El control estadístico de procesos requiere de una adecuada determinación de los límites de control para poder identificar variaciones inaceptables en un proceso. El establecimiento de estos límites se realiza generalmente utilizando la media y la desviación estándar del proceso, aunque existen otros métodos disponibles. La elección del método adecuado dependerá de las características del proceso y de los objetivos establecidos.
Qué medidas correctivas se pueden tomar cuando se detecta una variación fuera de los límites de control
El Control Estadístico de Procesos (CEP) es una metodología utilizada en la industria para mejorar la calidad y eficiencia de los procesos productivos. Su objetivo principal es controlar y mantener los parámetros de un proceso dentro de límites aceptables, detectando y corrigiendo cualquier desviación que pudiera afectar la calidad del producto final.
Una de las situaciones más comunes que pueden ocurrir durante el monitoreo de un proceso con CEP es detectar una variación fuera de los límites de control establecidos. Esto puede indicar que algo está sucediendo en el proceso que está generando resultados no deseados y que requiere ser analizado y corregido.
Cuando se detecta una variación fuera de los límites de control, es importante tomar medidas correctivas para identificar y solucionar el problema. Estas medidas pueden variar dependiendo de la naturaleza del proceso y la causa de la variación observada.
1. Identificar la causa raíz
Lo primero que se debe hacer cuando se detecta una variación fuera de los límites de control es identificar la causa raíz del problema. Esto implica analizar detalladamente los datos recopilados del proceso, así como realizar un análisis de causa-efecto para determinar qué factores podrían estar contribuyendo a la variación observada.
Una vez identificada la causa raíz, es posible tomar las medidas necesarias para corregir o eliminar el problema. Esto puede implicar ajustes en los parámetros del proceso, cambios en los materiales utilizados, modificaciones en los equipos o maquinarias, entre otras acciones.
2. Realizar ajustes en el proceso
Una vez identificada la causa raíz, es necesario realizar los ajustes correspondientes en el proceso para corregir la variación observada. Esto puede implicar modificar los parámetros de control del proceso, como por ejemplo la temperatura, la presión, el tiempo de ciclo, entre otros.
Es importante realizar estos ajustes de manera controlada y documentada, asegurándose de que se cumplan todos los requisitos establecidos en los procedimientos y normativas internas de la empresa. Además, es recomendable realizar un seguimiento continuo del proceso para verificar la efectividad de los ajustes realizados y asegurarse de que la variación se mantiene dentro de los límites aceptables.
3. Implementar acciones preventivas
Una vez corregido el problema y restablecido el control del proceso, es importante implementar acciones preventivas para evitar que la variación vuelva a ocurrir en el futuro. Estas acciones pueden incluir modificaciones en los procedimientos operativos, la capacitación del personal involucrado en el proceso, la implementación de nuevas tecnologías o metodologías de trabajo, entre otras.
La implementación de estas acciones preventivas tiene como objetivo mejorar la estabilidad y confiabilidad del proceso, minimizando así la probabilidad de que se produzcan desviaciones en el futuro.
4. Monitorear y evaluar continuamente
Una vez tomadas las medidas correctivas y preventivas, es fundamental monitorear y evaluar de manera continua el proceso para asegurarse de que se mantenga bajo control. Esto implica recopilar y analizar regularmente los datos del proceso, utilizando herramientas estadísticas y gráficos de control para detectar cualquier desviación temprana y poder tomar las acciones necesarias de inmediato.
Además, es recomendable establecer indicadores clave de desempeño (KPIs) para medir la eficiencia y calidad del proceso a lo largo del tiempo. Estos KPIs permitirán evaluar el impacto de las medidas implementadas y realizar ajustes adicionales si es necesario.
Cuando se detecta una variación fuera de los límites de control en un proceso, es importante tomar medidas correctivas para identificar y solucionar el problema. Esto incluye identificar la causa raíz, realizar ajustes en el proceso, implementar acciones preventivasy monitorear y evaluar continuamente el proceso para asegurarse de que se mantenga bajo control. El CEP proporciona las herramientas necesarias para lograr esto, mejorando así la calidad y eficiencia de la producción.
Cuáles son algunas estrategias para mantener un control estadístico de procesos efectivo a largo plazo
El control estadístico de procesos es una herramienta fundamental para las empresas que buscan mejorar su producción y eficiencia. A través del análisis de datos y la aplicación de técnicas estadísticas, es posible identificar y corregir desviaciones en los procesos de producción, minimizando así la variabilidad y maximizando la calidad del producto final.
Pero, ¿cómo podemos mantener un control estadístico de procesos efectivo a largo plazo? Aquí te presento algunas estrategias clave:
1. Establecer límites de control claros
Para asegurar un control efectivo, es necesario establecer límites de control claros para cada proceso. Estos límites se basan en el análisis estadístico de los datos históricos y representan los valores dentro de los cuales se considera que el proceso está bajo control. Establecer límites de control adecuados permite detectar de manera temprana cualquier desviación significativa y tomar medidas correctivas de inmediato.
2. Recopilar y analizar datos de forma regular
Es fundamental recopilar datos de forma regular y consistente para poder realizar un análisis estadístico adecuado. La frecuencia de recolección de datos puede variar dependiendo del tipo de proceso y sus características, pero es importante asegurarse de contar con suficiente información para identificar patrones y tendencias a lo largo del tiempo. Además, es crucial utilizar herramientas adecuadas para analizar estos datos, como gráficos de control y otras técnicas estadísticas.
3. Capacitar al personal en el uso del control estadístico de procesos
El control estadístico de procesos no puede ser efectivo si el personal encargado de llevarlo a cabo no cuenta con los conocimientos y habilidades necesarias. Es importante capacitar a los empleados en el uso de las herramientas y técnicas estadísticas pertinentes, para que puedan recolectar datos de manera adecuada, interpretar los resultados y tomar acciones correctivas cuando sea necesario. Asimismo, se deben promover prácticas de mejora continua y fomentar la cultura de calidad en toda la organización.
4. Realizar análisis de causa raíz
Cuando se detecta una desviación o un problema en el proceso, es fundamental realizar un análisis de causa raíz para identificar la(s) causa(s) principal(es) del problema. El análisis de causa raíz permite entender las razones detrás de las desviaciones y tomar acciones correctivas efectivas para prevenir su recurrencia en el futuro. Esta técnica puede involucrar el uso de herramientas como diagramas de causa-efecto, análisis de Pareto, entre otras.
5. Implementar mejoras continuas
El control estadístico de procesos es un proceso dinámico en el que siempre se busca la mejora continua. A medida que la empresa recopila y analiza datos, identifica oportunidades de mejora y toma acciones correctivas, se generan aprendizajes y se implementan cambios en el proceso para alcanzar niveles más altos de eficiencia y calidad. Es importante tener un sistema estructurado de gestión de mejoras continuas que permita detectar y aprovechar estas oportunidades.
Mantener un control estadístico de procesos efectivo a largo plazo requiere establecer límites de control claros, recopilar y analizar datos de forma regular, capacitar al personal adecuadamente, realizar análisis de causa raíz y promover mejoras continuas. Al implementar estas estrategias, las empresas pueden maximizar la calidad de sus productos, minimizando la variabilidad del proceso y optimizando su producción.
Cuáles son algunos ejemplos reales de implementación exitosa del control estadístico de procesos en diferentes industrias
El control estadístico de procesos (CEP) es una herramienta invaluable para mejorar la producción y garantizar la calidad en diferentes industrias. A través del análisis de datos recolectados durante el proceso de producción, el CEP brinda información precisa y en tiempo real sobre el desempeño de los procesos, lo que permite identificar y corregir problemas antes de que se conviertan en defectos o fallas.
Existen numerosos ejemplos reales de empresas que han implementado con éxito el CEP en sus operaciones, logrando mejoras significativas en la eficiencia, productividad y calidad. A continuación, exploraremos algunos de estos casos en diferentes industrias:
1. Industria manufacturera
En la industria manufacturera, el CEP ha demostrado ser especialmente útil para controlar y optimizar los procesos de producción. Por ejemplo, una empresa de fabricación de automóviles implementó el CEP en su línea de ensamblaje para monitorear la calidad de las piezas y detectar posibles desviaciones en los estándares de producción. Gracias a la detección temprana de problemas, pudieron realizar ajustes rápidos y minimizar el número de productos no conformes, mejorando así la eficiencia y reduciendo los costos de retrabajo.
2. Sector farmacéutico
En la industria farmacéutica, el CEP tiene un papel fundamental en garantizar la seguridad y calidad de los medicamentos. Una empresa farmacéutica implementó el CEP en su proceso de fabricación de medicamentos, monitorizando parámetros críticos como la dosificación y el tiempo de mezcla. Esto les permitió identificar y corregir desviaciones rápidamente, asegurando que los medicamentos cumplieran con los estándares de calidad establecidos por las autoridades reguladoras.
3. Industria alimentaria
La industria alimentaria también se ha beneficiado del uso del CEP para mejorar la calidad y seguridad de los alimentos. Por ejemplo, una empresa de procesamiento de alimentos implementó el CEP en su línea de producción de carne, monitoreando constantemente la temperatura, la humedad y otros parámetros críticos. Gracias a esto, pudieron prevenir la proliferación de bacterias y evitar posibles casos de contaminación alimentaria, garantizando la seguridad del producto final.
4. Sector de servicios
Aunque el CEP es más comúnmente asociado con la industria manufacturera, también puede aplicarse con éxito en el sector de servicios. Por ejemplo, un centro de llamadas implementó el CEP para monitorear la calidad de las interacciones entre los agentes de servicio al cliente y los clientes. Al analizar datos sobre la duración de las llamadas, el nivel de satisfacción del cliente y otras métricas clave, pudieron identificar áreas de mejora y brindar capacitación adicional a los agentes, lo que resultó en un aumento significativo en la satisfacción del cliente y en la eficiencia operativa.
Estos son solo algunos ejemplos de cómo diferentes industrias han implementado exitosamente el control estadístico de procesos para mejorar su producción. En todos estos casos, el CEP ha demostrado ser una herramienta poderosa para identificar y corregir problemas, garantizando la calidad de los productos o servicios y mejorando la eficiencia en general.
Preguntas frecuentes (FAQ)
1. ¿Qué es el Control Estadístico de Procesos?
El Control Estadístico de Procesos (CEP) es una metodología que permite analizar y monitorear la estabilidad y capacidad de un proceso productivo, a través del análisis estadístico de los datos obtenidos durante la producción.
2. ¿Cuál es el objetivo del CEP?
El objetivo del CEP es identificar las variaciones que ocurren en un proceso, para poder tomar acciones correctivas y preventivas con el fin de mejorar la calidad, reducir costos y aumentar la eficiencia en la producción.
3. ¿Cuáles son las principales herramientas utilizadas en el CEP?
Algunas de las herramientas utilizadas en el CEP son: gráficos de control, histogramas, diagramas de Pareto, diagramas de dispersión, entre otros. Estas herramientas permiten visualizar y analizar los datos recolectados para tomar decisiones informadas.
4. ¿Cómo se implementa el CEP en una empresa?
La implementación del CEP implica definir los indicadores de calidad relevantes, recolectar y analizar los datos, establecer límites de control y tomar acciones cuando se detectan desviaciones o patrones inusuales en los procesos. También es importante contar con personal capacitado y utilizar software especializado.
5. ¿Cuáles son los beneficios del CEP?
Entre los beneficios del CEP destacan la mejora en la calidad del producto o servicio, la reducción de los defectos y reprocesos, la optimización de los recursos, el aumento de la productividad y la satisfacción del cliente.
Deja una respuesta
Entradas relacionadas