Transductor de presión: Todo lo que necesitas saber sobre esta tecnología imprescindible
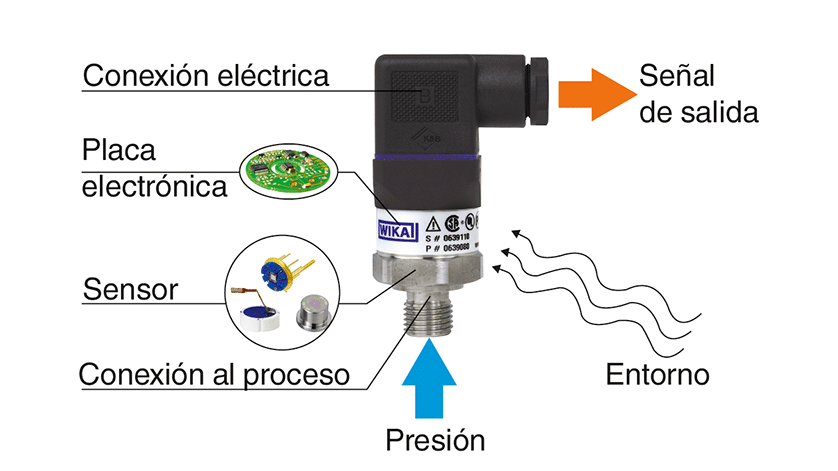
Los transductores de presión son dispositivos fundamentales en una amplia gama de aplicaciones industriales y comerciales. Estos dispositivos se utilizan para medir con precisión la presión de diferentes fluidos, como líquidos y gases, y convertir esta información en una señal eléctrica que puede ser monitoreada o controlada por otros equipos.
Exploraremos cómo funcionan los transductores de presión, qué tipos de transductores existen, las aplicaciones más comunes en las que se utilizan y algunos consejos importantes a tener en cuenta al seleccionar y utilizar estos dispositivos. También veremos las ventajas y desventajas de los transductores de presión y cuáles son las consideraciones clave a la hora de elegir el transductor adecuado para tu aplicación específica. ¡Sigue leyendo para descubrir todo lo que necesitas saber sobre esta tecnología imprescindible!
- Qué es un transductor de presión y cómo funciona
- Cuál es la importancia de los transductores de presión en diferentes industrias
- Cuáles son las características clave de los transductores de presión y cómo se diferencian de otros dispositivos de medición
- Cuáles son los principales tipos de transductores de presión y cómo se utilizan en aplicaciones específicas
- Cómo elegir el transductor de presión adecuado para mi aplicación
- Cuáles son las ventajas y limitaciones de los transductores de presión
- Cuáles son las principales tecnologías utilizadas en los transductores de presión y cuál es su relevancia en función de la aplicación
- Es necesario calibrar los transductores de presión y con qué frecuencia se debe hacer
- Cómo mantener y prolongar la vida útil de los transductores de presión
- Cuáles son las tendencias emergentes en la tecnología de transductores de presión
- Preguntas frecuentes (FAQ)
Qué es un transductor de presión y cómo funciona
Un transductor de presión es un dispositivo utilizado para medir la presión de un fluido o gas y convertirlo en una señal eléctrica proporcional. Es una tecnología ampliamente utilizada en diversas industrias, desde la automotriz hasta la aeroespacial, pasando por la medicina y la energía.
El funcionamiento básico de un transductor de presión se basa en el principio de deformación mecánica. Cuando se aplica una presión al transductor, este experimenta una deformación que se traduce en un cambio en su resistencia eléctrica. Este cambio de resistencia se convierte en una señal eléctrica, que puede ser amplificada y procesada para obtener la lectura de presión precisa.
Tipos de transductores de presión
Existen varios tipos de transductores de presión, cada uno diseñado para adaptarse a diferentes aplicaciones y requerimientos específicos.
- Transductores de presión piezorresistivos: son los más comunes y utilizados en muchas aplicaciones industriales. Estos transductores utilizan una membrana flexible con sensores de resistencia que varían su valor cuando se someten a presión. Son precisos y confiables, y se pueden encontrar en dispositivos como manómetros y transmisores de presión.
- Transductores capacitivos: estos transductores utilizan cambios en la capacitancia producidos por la deformación de una membrana dieléctrica para medir la presión. Son especialmente adecuados para aplicaciones de alta precisión y baja presión.
- Transductores de presión magnetostrictivos: en estos transductores, la presión aplicada produce una variación en la longitud de una varilla magnética. Esta variación se traduce en un cambio en la frecuencia de resonancia, que se utiliza para determinar la presión.
- Transductores de presión piezoeléctricos: utilizan cristales piezoeléctricos que generan una carga eléctrica cuando se someten a presión. Estos transductores son altamente sensibles y se utilizan en aplicaciones donde se requiere una detección extremadamente precisa.
Cada tipo de transductor de presión tiene sus ventajas y desventajas, y es importante seleccionar el adecuado según las necesidades específicas de la aplicación.
Aplicaciones de los transductores de presión
Los transductores de presión son esenciales en una amplia gama de aplicaciones donde es necesario medir y controlar la presión de manera precisa.
- En la industria automotriz, los transductores de presión se utilizan para medir la presión del aceite del motor y del sistema de combustible, así como para controlar los sistemas de frenos y suspensión.
- En la industria aeroespacial, los transductores de presión se utilizan para medir la presión del aire y de los fluidos en aviones y cohetes, asegurando un funcionamiento seguro de los sistemas.
- En la industria médica, los transductores de presión son fundamentales para medir y controlar la presión sanguínea, así como para monitorear la presión en dispositivos de ventilación y en equipos de diálisis.
- En la industria energética, los transductores de presión se utilizan para medir la presión en sistemas hidráulicos y neumáticos, así como en procesos de producción de energía como la generación de vapor y la perforación de pozos de petróleo.
Estos son solo algunos ejemplos de las muchas aplicaciones en las que se utilizan los transductores de presión. Su precisión y confiabilidad los convierten en una tecnología imprescindible en numerosos campos.
Cuál es la importancia de los transductores de presión en diferentes industrias
Los transductores de presión desempeñan un papel fundamental en numerosas industrias. Estos dispositivos han revolucionado la forma en que medimos la presión en diferentes entornos y aplicaciones. Desde la industria manufacturera hasta la industria médica, los transductores de presión son una tecnología imprescindible para garantizar una medición precisa y confiable.
En la industria automotriz, por ejemplo, los transductores de presión juegan un papel crucial en el monitoreo y control del sistema de combustible. Estos dispositivos miden con precisión la presión del sistemas de inyección de combustible, lo que permite una mezcla adecuada de aire y combustible en el motor. Esto no solo mejora el rendimiento del vehículo, sino que también reduce las emisiones contaminantes.
En la industria farmacéutica, los transductores de presión son esenciales para garantizar la calidad y seguridad de los productos. En la fabricación de medicamentos, por ejemplo, estos dispositivos se utilizan para medir la presión en los reactores y recipientes de almacenamiento, asegurando así que los procesos se realicen dentro de los parámetros adecuados. De esta manera, se evitan problemas como contaminaciones o reacciones indeseadas que podrían poner en peligro la salud de los pacientes.
La industria aeroespacial también depende en gran medida de los transductores de presión. Estos dispositivos se utilizan en aviones y cohetes para medir la presión en el interior de los tanques de combustible, los sistemas hidráulicos y los motores, entre otros componentes críticos. Una medición precisa y confiable de la presión es fundamental para garantizar la seguridad y el rendimiento de estas aeronaves.
En la industria de procesos, los transductores de presión son fundamentales para controlar y monitorear la presión en diversas aplicaciones. Desde la industria química hasta la producción de alimentos y bebidas, estos dispositivos se utilizan para garantizar que los procesos se lleven a cabo bajo las condiciones adecuadas. Esto permite no solo un mayor control de calidad, sino también una mejora en la eficiencia y productividad de estas industrias.
Principales tipos de transductores de presión
Existen diferentes tipos de transductores de presión, cada uno con sus características y aplicaciones específicas. Algunos de los más comunes incluyen:
Transductores de presión piezorresistivos:
Estos transductores utilizan la variación de resistencia eléctrica en un material sensible a la presión para realizar la medición. Son muy precisos y se utilizan en una amplia gama de aplicaciones.Transductores de presión capacitivos:
En estos transductores, la presión actúa sobre una membrana flexible que cambia la distancia entre dos placas, lo que produce una variación en la capacidad eléctrica. Son ideales para aplicaciones que requieren alta precisión y estabilidad a largo plazo.Transductores de presión de película delgada:
Estos transductores utilizan una película delgada de material sensible a la presión que cambia su resistencia cuando se somete a presión. Son compactos y adecuados para aplicaciones en espacios reducidos.Transductores de presión resonantes:
En estos transductores, la presión se convierte en una señal acústica, que luego se mide y se relaciona con la presión. Se utilizan en aplicaciones donde se requiere una alta frecuencia de medición.
Estos son solo algunos ejemplos de los diferentes tipos de transductores de presión disponibles en el mercado. Cada tipo tiene sus ventajas y desventajas, y la elección del más adecuado dependerá de las necesidades específicas de cada aplicación.
Cuáles son las características clave de los transductores de presión y cómo se diferencian de otros dispositivos de medición
Los transductores de presión son dispositivos esenciales en la industria moderna, ya que permiten medir y controlar con precisión la presión en una amplia gama de aplicaciones. Estos dispositivos se utilizan en una variedad de sectores, como la industria automotriz, la aeroespacial, la petroquímica y la medicina, entre otros.
Una de las características clave de los transductores de presión es su capacidad para convertir una presión física en una señal eléctrica proporcional. Esto significa que estos dispositivos pueden medir un rango específico de presiones y transmitir esa información de manera precisa y confiable a otros dispositivos o sistemas.
A diferencia de otros dispositivos de medición, como los manómetros o los barómetros, los transductores de presión ofrecen ventajas significativas. Por ejemplo, los transductores de presión son más precisos y más versátiles, ya que pueden medir una amplia gama de presiones y adaptarse a diferentes condiciones de trabajo.
Cómo funciona un transductor de presión
Para comprender cómo funcionan los transductores de presión, es importante conocer su estructura interna. Básicamente, estos dispositivos constan de dos componentes principales: una membrana sensible a la presión y un circuito electrónico.
La membrana sensible a la presión es una delgada lámina flexible que se deforma en respuesta a los cambios de presión. Esta deformación genera una señal eléctrica proporcional a la presión aplicada. La precisión de esta señal depende de la sensibilidad y la calibración de la membrana.
El circuito electrónico del transductor de presión se encarga de amplificar y acondicionar la señal generada por la membrana sensible a la presión. Este circuito convierte la señal analógica en una señal digital para su procesamiento y transmisión.
Existen diferentes tipos de transductores de presión, como los transductores piezoeléctricos, los transductores capacitivos y los transductores de resistencia. Cada uno de estos tipos utiliza un principio de funcionamiento diferente, pero todos comparten el objetivo común de medir con precisión la presión.
Aplicaciones de los transductores de presión
Los transductores de presión son ampliamente utilizados en numerosas aplicaciones, gracias a su capacidad para medir y controlar la presión. Algunas de las aplicaciones más comunes incluyen:
- Sistemas de control y monitoreo industrial: los transductores de presión se utilizan para controlar y monitorear la presión en sistemas industriales, como los sistemas hidráulicos o neumáticos. Esto permite asegurar que estos sistemas funcionen correctamente y evitar posibles fallos o daños.
- Petróleo y gas: en la industria petrolera y gasífera, los transductores de presión se utilizan para medir la presión en pozos, tuberías y equipos relacionados. Esto es crucial para garantizar la seguridad y eficiencia de las operaciones en este sector.
- Vehículos automotrices: los transductores de presión son fundamentales en los sistemas de control de motores, así como en los sistemas de frenado. Estos dispositivos permiten medir la presión del combustible, el aceite y otros fluidos esenciales para el funcionamiento de un vehículo.
- Medicina y salud: en el campo de la medicina, los transductores de presión se utilizan para medir la presión arterial, la presión intracraneal y otras variables fisiológicas. Estos dispositivos son cruciales para el diagnóstico y seguimiento de diversas enfermedades y condiciones médicas.
Los transductores de presión son tecnologías imprescindibles en numerosas industrias y aplicaciones. Gracias a su capacidad para medir y controlar la presión con precisión, estos dispositivos permiten mejorar la eficiencia, seguridad y calidad en una amplia gama de procesos y sistemas.
Cuáles son los principales tipos de transductores de presión y cómo se utilizan en aplicaciones específicas
Los transductores de presión son dispositivos esenciales en diversas industrias y aplicaciones donde se requiere medir y controlar la presión de forma precisa. Existen diferentes tipos de transductores de presión, cada uno con características y usos específicos según las necesidades de cada aplicación.
1. Transductores de presión piezorresistivos
Los transductores de presión piezorresistivos utilizan el principio de transmisión de presión a través de una membrana sensible. Estos transductores están compuestos por un puente de resistencias que varía su resistencia eléctrica en función de la deformación de la membrana sensible a la presión. Este cambio de resistencia se convierte en una señal eléctrica proporcional a la presión aplicada.
Estos transductores son especialmente adecuados para medir presiones estáticas y dinámicas en aplicaciones industriales, como la monitorización de la presión en sistemas de ventilación, monitoreo de procesos químicos y control de presión en sistemas hidráulicos.
2. Transductores de presión capacitivos
Los transductores de presión capacitivos están basados en el principio de variación de capacidad eléctrica en función de la presión aplicada. Estos transductores cuentan con una cavidad de referencia llena de gas o vacío y una cavidad sensible a la presión. Al aplicar una presión sobre la cavidad sensible, se modifica la capacidad eléctrica entre ambas cavidades y se genera una señal eléctrica proporcional a la presión ejercida.
Estos transductores se utilizan en aplicaciones de baja presión y alta precisión, como el control de presión en sistemas de climatización, medición de presión en calibradores de instrumentación y monitorización de presión en equipos médicos.
3. Transductores de presión resonantes
Los transductores de presión resonantes se basan en el principio de resonancia mecánica de una estructura cuando se aplica una presión. Estos transductores operan mediante la vibración de un elemento resonante, como un cristal de cuarzo, que varía su frecuencia de resonancia en función de la presión ejercida. Este cambio en la frecuencia es detectado y convertido en una señal eléctrica proporcional a la presión.
Estos transductores son especialmente utilizados en aplicaciones que requieren alta sensibilidad y estabilidad a largo plazo, como el monitoreo de presión en sistemas aeroespaciales, pruebas de laboratorio y medición de presión en meteorología.
4. Transductores de presión piezoeléctricos
Los transductores de presión piezoeléctricos funcionan mediante el efecto piezoeléctrico, el cual consiste en la generación de una carga eléctrica cuando se aplica una presión sobre ciertos materiales. Estos transductores están compuestos por cristales o cerámicas piezoeléctricas que generan una señal eléctrica proporcional a la presión ejercida.
Este tipo de transductores se emplea en aplicaciones que requieren alta velocidad de respuesta y resolución, como el monitoreo de presión en sistemas neumáticos y medición de presión en procesos industriales de alta velocidad.
La elección del tipo de transductor de presión dependerá de las características específicas de cada aplicación, como la gama de presiones a medir, la precisión requerida y las condiciones ambientales. Gracias a estos dispositivos, se logra obtener información precisa y confiable sobre la presión en una amplia variedad de aplicaciones industriales y científicas.
Cómo elegir el transductor de presión adecuado para mi aplicación
La elección del transductor de presión adecuado para tu aplicación es crucial para garantizar mediciones precisas y confiables. Con la amplia variedad de opciones disponibles en el mercado, puede resultar abrumador tomar una decisión informada. Sin embargo, al tener en cuenta algunos factores clave, puedes elegir el transductor de presión que mejor se adapte a tus necesidades.
Rango de presión
Uno de los primeros aspectos a considerar es el rango de presión que necesitas medir. Los transductores de presión están diseñados para medir diferentes gamas de presión, desde bajas hasta altas. Es importante identificar cuál es la presión máxima y mínima que esperas medir en tu aplicación y asegurarte de que el transductor seleccionado pueda cubrir este rango sin problemas. Además, ten en cuenta si necesitas una alta resolución en la medición o si un rango más amplio es más importante para tu aplicación.
Tipo de presión
Otro factor relevante es el tipo de presión que deseas medir. Los transductores de presión pueden clasificarse en tres categorías principales: presión absoluta, presión relativa y presión diferencial. La presión absoluta mide con referencia al cero absoluto, mientras que la presión relativa mide con referencia a la presión atmosférica. Por otro lado, la presión diferencial mide la diferencia de presión entre dos puntos. Es fundamental determinar qué tipo de presión necesitas medir para elegir el transductor adecuado.
Compatibilidad con el medio
El medio en el que se encontrará el transductor de presión también es un factor clave a tener en cuenta. Algunas aplicaciones pueden requerir transductores que sean compatibles con líquidos corrosivos o agresivos, mientras que otras pueden requerir transductores aptos para gases o ambientes de alta temperatura. Asegúrate de verificar las especificaciones técnicas del transductor para asegurarte de que sea compatible con el medio en el que trabajará.
Salida del transductor
Otra consideración importante es el tipo de salida que ofrece el transductor de presión. La salida puede ser analógica, como voltaje o corriente, o digital, como una señal en serie o bus de comunicación. La elección dependerá de la compatibilidad de la salida con tu sistema de adquisición de datos o control. Además, algunos transductores de presión también ofrecen funciones adicionales, como compensación de temperatura o capacidades de calibración, lo cual puede ser beneficioso dependiendo de tus necesidades específicas.
<ul>
<li>Rango de presión requerido para tu aplicación.</li>
<li>Tipo de presión que deseas medir (absoluta, relativa o diferencial).</li>
<li>Compatibilidad con el medio en el que trabajará el transductor.</li>
<li>Tipo de salida del transductor y su compatibilidad con tu sistema.</li>
</ul>
Cuáles son las ventajas y limitaciones de los transductores de presión
Los transductores de presión, también conocidos como sensores de presión, son dispositivos electrónicos esenciales en una amplia gama de aplicaciones industriales, médicas y automotrices. Estos dispositivos tienen la capacidad de convertir una señal de presión o fuerza en una señal eléctrica proporcional, lo que permite medir y monitorear con precisión la presión en diferentes entornos.
Una de las principales ventajas de los transductores de presión es su alta precisión y exactitud en la medición de la presión. Esto los convierte en una herramienta confiable para controlar procesos críticos en la industria, como la producción de alimentos y bebidas, la fabricación de productos farmacéuticos y la monitorización de sistemas hidráulicos y neumáticos.
Otra ventaja importante de los transductores de presión es su capacidad para medir tanto presiones estáticas como dinámicas. Esto significa que pueden manejar cambios rápidos en la presión sin comprometer la precisión de la medición. Esta característica es especialmente valiosa en aplicaciones donde se producen fluctuaciones frecuentes de la presión, como en sistemas de frenado en vehículos o en máquinas de soplado.
Además de su precisión y capacidad para medir presiones dinámicas, los transductores de presión también ofrecen una excelente resistencia a condiciones adversas, como altas temperaturas, líquidos corrosivos y entornos hostiles. Estos dispositivos están diseñados para soportar ambientes difíciles sin comprometer su rendimiento, lo que los hace altamente confiables en entornos industriales exigentes.
A pesar de las numerosas ventajas que ofrecen los transductores de presión, también existen algunas limitaciones a considerar. Una de ellas es su sensibilidad a las vibraciones y a los cambios bruscos en la presión. En entornos con actividad sísmica o con fluctuaciones frecuentes de la presión, es posible que se produzcan mediciones inexactas o que el dispositivo se dañe.
Otra limitación común de los transductores de presión es su rango de medición. Cada dispositivo tiene su propio rango de operación específico, que puede no ser adecuado para todas las aplicaciones. Es importante seleccionar el transductor de presión correcto en función de la presión máxima esperada en el sistema para garantizar mediciones precisas y confiables.
Los transductores de presión son tecnologías imprescindibles en diversas industrias debido a su alta precisión, capacidad para medir presiones estáticas y dinámicas, resistencia a condiciones adversas y confiabilidad en entornos exigentes. Sin embargo, es importante tener en cuenta sus limitaciones, como la sensibilidad a las vibraciones y los cambios bruscos de presión, así como su rango de medición específico para cada aplicación.
Cuáles son las principales tecnologías utilizadas en los transductores de presión y cuál es su relevancia en función de la aplicación
Los transductores de presión son dispositivos esenciales en una amplia gama de aplicaciones industriales y científicas. Estos dispositivos se utilizan para medir la presión de fluidos y gases en diferentes entornos, lo que permite monitorear y controlar procesos críticos en diversas industrias.
Para comprender mejor el funcionamiento de los transductores de presión, es importante conocer las principales tecnologías utilizadas en su fabricación y entender cómo estas tecnologías afectan su rendimiento y precisión.
Tecnología piezoeléctrica
Una de las tecnologías más comunes utilizadas en los transductores de presión es la tecnología piezoeléctrica. Este tipo de sensor utiliza cristales piezoeléctricos que generan una carga eléctrica cuando se someten a esfuerzos mecánicos, como la presión ejercida por un fluido o gas.
La tecnología piezoeléctrica ofrece una alta sensibilidad y una respuesta rápida a los cambios de presión. Además, estos transductores son muy robustos y pueden operar en condiciones extremas, como altas temperaturas o ambientes hostiles.
Tecnología capacitiva
Otra tecnología comúnmente utilizada en los transductores de presión es la tecnología capacitiva. Estos sensores aprovechan el principio de cambio de capacitancia para medir la presión.
En un transductor de presión capacitivo, hay dos placas metálicas separadas por una capa dieléctrica. Cuando se aplica una presión sobre la placa, la distancia entre las placas cambia, lo que a su vez afecta la capacitancia del dispositivo. La variación de la capacitancia se convierte en una señal eléctrica proporcional a la presión aplicada.
La tecnología capacitiva ofrece una alta precisión y estabilidad a largo plazo. Estos transductores son ampliamente utilizados en aplicaciones donde se requiere una medición precisa y estable de la presión, como en instrumentos de laboratorio o dispositivos médicos.
Tecnología resistiva
La tecnología resistiva es otra opción común en los transductores de presión. En estos sensores, se utiliza un elemento sensible a la presión que cambia su resistencia eléctrica en respuesta a la deformación mecánica producida por la presión.
El elemento sensible a la presión puede ser una lámina metálica o un cable enrollado en forma de espiral. Cuando se aplica una presión, el elemento sensible se deforma, lo que a su vez cambia su resistencia eléctrica. Este cambio de resistencia se mide y se convierte en una señal de salida proporcionales a la presión ejercida.
Los transductores de presión basados en la tecnología resistiva ofrecen una buena linealidad y una amplia gama de rangos de presión. Son ampliamente utilizados en aplicaciones industriales, como el control de procesos de fabricación o la monitorización de sistemas hidráulicos.
Aunque estas tres tecnologías son las más utilizadas en los transductores de presión, existen otras, como los transductores de estado sólido que utilizan tecnologías ópticas o de semiconductor para medir la presión. Cada una de estas tecnologías tiene sus propias características y se utiliza en función de los requisitos específicos de la aplicación.
Los transductores de presión son componentes esenciales en muchas aplicaciones industriales y científicas. La elección de la tecnología adecuada depende de factores como la precisión requerida, el rango de presión y las condiciones de operación. Comprender las principales tecnologías utilizadas en estos dispositivos permite tomar decisiones informadas al seleccionar un transductor de presión para una aplicación específica.
Es necesario calibrar los transductores de presión y con qué frecuencia se debe hacer
Los transductores de presión son dispositivos esenciales en aplicaciones que requieren la medición y control precisa de la presión. Sin embargo, para garantizar su correcto funcionamiento, es necesario calibrarlos periódicamente.
La calibración de los transductores de presión consiste en comparar su salida con una fuente de referencia conocida y ajustar los valores si es necesario. Este proceso ayuda a asegurar que la lectura del transductor sea precisa y confiable.
¿Con qué frecuencia se debe calibrar un transductor de presión?
La frecuencia de calibración de un transductor de presión depende de varios factores, como la precisión requerida, el entorno de uso y las regulaciones aplicables. En general, se recomienda realizar la calibración al menos una vez al año o antes de cada uso crítico.
Es importante tener en cuenta que algunos transductores pueden requerir una calibración más frecuente debido a condiciones de operación extremas o desgaste. Por ejemplo, en entornos donde hay cambios bruscos de temperatura o vibraciones severas, se puede requerir una calibración más regular para mantener la precisión.
Proceso de calibración de un transductor de presión
El proceso de calibración de un transductor de presión involucra varias etapas para garantizar resultados precisos. Estas etapas pueden incluir:
- Preparación: Antes de iniciar la calibración, es importante verificar que el transductor esté limpio y en buen estado. También se deben revisar las condiciones ambientales, como la temperatura y la presión atmosférica.
- Comparación con una referencia: El siguiente paso es comparar la salida del transductor con una fuente de referencia calibrada. Esto se puede hacer utilizando equipos de calibración específicos, como manómetros o calibradores de presión.
- Ajuste y corrección: Si se detectan desviaciones en la salida del transductor, se deben realizar ajustes y correcciones necesarias para alinear las lecturas. Estos ajustes pueden incluir cambios en la configuración electrónica del transductor o el uso de dispositivos externos de ajuste.
- Verificación final: Una vez realizados los ajustes, se debe verificar nuevamente la salida del transductor para asegurar que esté dentro del rango de precisión requerido. Esto se puede hacer comparando nuevamente con la fuente de referencia o utilizando métodos estadísticos y análisis de datos.
Es fundamental seguir los procedimientos de calibración recomendados por el fabricante del transductor y utilizar equipos adecuados para garantizar resultados confiables y precisos. Además, es importante mantener registros de calibración detallados que incluyan fechas, técnicas utilizadas y resultados obtenidos.
La calibración regular de los transductores de presión es esencial para mantener su rendimiento y precisión. La frecuencia de calibración debe determinarse según factores como la precisión requerida y las condiciones de operación. Seguir los procedimientos recomendados y mantener registros precisos son prácticas clave para garantizar resultados confiables en la medición de presión.
Cómo mantener y prolongar la vida útil de los transductores de presión
El transductor de presión es una tecnología esencial en diversos campos, ya que permite medir la presión en sistemas y procesos industriales. Sin embargo, para garantizar su funcionamiento óptimo y prolongar su vida útil, es importante seguir algunas recomendaciones de mantenimiento.
Limpieza regular
Una de las formas más sencillas de mantener los transductores de presión en buen estado es realizar una limpieza regular. Esto implica eliminar cualquier suciedad o contaminante que pueda acumularse en la superficie del transductor.
Para ello, se recomienda utilizar un paño suave o una brocha de cerdas finas para quitar el polvo y la suciedad superficial. En caso de que sea necesario, también se puede utilizar un líquido de limpieza suave, evitando siempre el contacto con componentes electrónicos sensibles.
Protección contra la humedad y ambientes corrosivos
Los transductores de presión son sensibles a la humedad y a los ambientes corrosivos, por lo que es fundamental protegerlos adecuadamente. Si se utilizan en áreas donde existe una alta concentración de humedad o se trabaja con sustancias corrosivas, se deben tomar medidas adicionales de protección.
Una opción es utilizar fundas protectoras o carcasas especiales que ayuden a evitar el ingreso de humedad y protejan al transductor de posibles daños. Además, es importante realizar inspecciones periódicas para detectar cualquier signo de corrosión y tomar las medidas necesarias para detener su avance.
Calibración regular
La calibración regular de los transductores de presión es fundamental para asegurar la precisión de las mediciones. Con el tiempo, estos dispositivos pueden sufrir desviaciones en su respuesta, por lo que es necesario ajustarlos periódicamente.
Para llevar a cabo la calibración, se pueden utilizar equipos especializados o recurrir a servicios de calibración externos. Durante este proceso, se comparará la lectura del transductor con un estándar conocido, y se realizarán los ajustes necesarios para corregir cualquier desviación.
Evitar sobrepresiones
Las sobrepresiones repentinas o prolongadas pueden dañar permanentemente los transductores de presión. Por lo tanto, es importante evitar aplicar presiones superiores a las especificadas por el fabricante o a las capacidades técnicas del dispositivo.
En caso de trabajar con sistemas o procesos que puedan generar sobrepresiones, se deben instalar válvulas de alivio o dispositivos de protección adecuados para evitar daños en el transductor. Además, es recomendable monitorear constantemente las presiones para identificar cualquier variación anormal y tomar acciones preventivas.
Siguiendo estas recomendaciones, podrás mantener tus transductores de presión en óptimas condiciones y prolongar su vida útil. Recuerda siempre consultar las especificaciones y recomendaciones del fabricante para obtener los mejores resultados y evitar daños innecesarios.
Cuáles son las tendencias emergentes en la tecnología de transductores de presión
En la era actual de la tecnología en constante avance, los transductores de presión se han convertido en una parte crucial de muchos sistemas y aplicaciones. Estos dispositivos desempeñan un papel fundamental en la medición precisa de la presión y ayudan a garantizar el correcto funcionamiento de numerosos procesos industriales y comerciales.
Al mirar hacia el futuro, es interesante observar las tendencias emergentes en la tecnología de los transductores de presión. A medida que la demanda de mayor precisión, confiabilidad y eficiencia aumenta, los fabricantes están innovando constantemente para satisfacer estas necesidades cambiantes. A continuación, exploraremos algunas de las tendencias más destacadas en esta área.
1. Miniaturización
Una de las tendencias clave en la tecnología de transductores de presión es la miniaturización. Los avances en microelectrónica y la miniaturización de los componentes electrónicos están permitiendo el desarrollo de transductores de presión cada vez más pequeños sin comprometer su rendimiento. Esta miniaturización ha abierto la puerta a nuevas aplicaciones donde el espacio es limitado, como en los dispositivos médicos implantables y los sistemas portátiles.
2. Mayor precisión
Otra tendencia importante es la búsqueda de una mayor precisión en la medición de la presión. Los transductores de presión con una precisión mejorada son cada vez más demandados en sectores como la industria automotriz, la aeronáutica y la industria alimentaria, donde la exactitud de las mediciones es esencial. Los avances en tecnología de sensores y la implementación de algoritmos de corrección de errores están permitiendo incrementar la precisión de estos dispositivos.
3. Tecnología inalámbrica
La tecnología inalámbrica también está impactando en el campo de los transductores de presión. La capacidad de transmitir datos de manera remota sin necesidad de cables ofrece ventajas significativas en términos de instalación, flexibilidad y mantenimiento. Los transductores de presión inalámbricos son especialmente útiles en entornos donde las conexiones por cable no son factibles o representan un riesgo.
4. Mayor resistencia a condiciones adversas
Los transductores de presión cada vez se utilizan en aplicaciones más exigentes en términos de condiciones ambientales. La demanda de mayor resistencia a vibraciones, choques, temperaturas extremas y ambientes corrosivos continúa creciendo. Los fabricantes están desarrollando transductores de presión robustos que pueden soportar estas condiciones adversas sin comprometer su rendimiento.
5. Integración con sistemas inteligentes
Con el auge del Internet de las cosas (IoT) y los sistemas inteligentes, los transductores de presión también están evolucionando para adaptarse a esta nueva realidad. La capacidad de integrarse con sistemas de monitoreo remoto, análisis de datos y control automatizado brinda una mayor eficiencia operativa y la posibilidad de tomar decisiones basadas en datos en tiempo real. Los transductores de presión inteligentes están revolucionando la forma en que se gestionan los procesos industriales y comerciales.
Las tendencias emergentes en la tecnología de los transductores de presión incluyen la miniaturización, mayor precisión, tecnología inalámbrica, mayor resistencia a condiciones adversas e integración con sistemas inteligentes. Estas tendencias están impulsando avances significativos en la industria, permitiendo aplicaciones más sofisticadas y mejorando la eficiencia y confiabilidad de los procesos donde se utilizan estos dispositivos indispensables.
Preguntas frecuentes (FAQ)
1. ¿Qué es un transductor de presión?
Es un dispositivo que convierte la presión aplicada sobre él en una señal eléctrica proporcional.
2. ¿Para qué se utiliza un transductor de presión?
Se utiliza para medir y controlar la presión en diferentes sistemas, como en la industria, automóviles y equipos médicos.
3. ¿Cuáles son los tipos de transductores de presión más comunes?
Los más comunes son los piezorresistivos, capacitivos y de membrana.
4. ¿Cuál es la diferencia entre un transductor de presión absoluta y uno relativa?
El transductor de presión absoluta mide la presión en relación a un vacío absoluto, mientras que el transductor relativo lo hace en relación a la presión atmosférica.
5. ¿Cómo se calibra un transductor de presión?
Se calibra comparando las salidas del transductor con una referencia estándar conocida y ajustando si es necesario.
Deja una respuesta
Entradas relacionadas